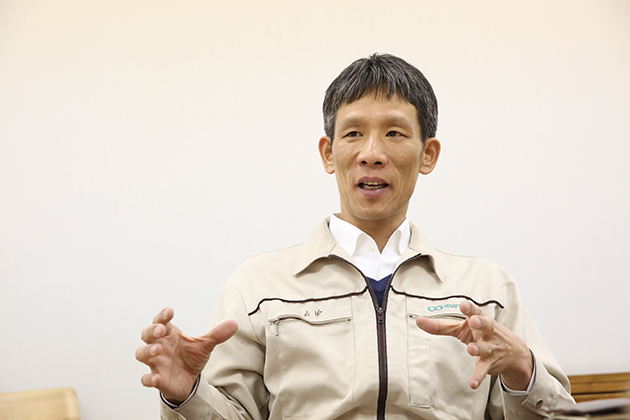
Interview: President Yamanaka
JAPANTWO(JP2):What does name "Maruni" mean?
President Yamanaka (Mr. Yamanaka):In the 3rd year of Showa era (1928), when the company was established, we were called "Showa Wood-Bending Factory". In Showa 8 (1933), two companies merged. Hoping for the companies to work together in unison, it is said that they came up with the name "Maruni" (two circles). Back then, there weren't many company names in Katakana characters, so it was considered a very stylish name.
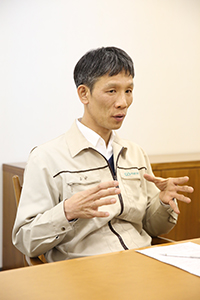
JP2:Could you also tell us why "Wood Industry" was included in the name?
Mr. Yamanaka:The founder was from Miyajima in Hiroshima prefecture. This place is known for shrines constructed by the skilled Miyadaiku (Shrine carpenters) and there are still many shrines left to this day, such as the Itsukushima shrine. Since early in his childhood, he grew up in an environment surrounded by nature and historical wooden structures, so it seems like he naturally got interested in crafting things out of wood.
Also the founder loved machines from early on, and was deeply interested in the manufacturing industry. Once he had decided making furniture using wood, he imported machines from Germany and USA, which was quite uncommon in Japan at that time, and began to modify them, increasing the efficiency of furniture production. Many of the modified-machines have been preserved and are still in good use up to this day. He acquired German by himself, in order to learn about the machines. He must have had tremendous amount of passion for wooden products and machines. That is how "Wood Industry" came to be included.
JP2:How old are the machines that are still being in use?
Mr. Yamanaka:The oldest ones are over 50 years old. There are machines that are as old as I am, and are still working hard at the front line.
JP2:It's amazing to hear that they are being in use for over 50 years. Maruni Wood Industry's technical skills for furniture production and machine modification, at the time, must have been excellent.
Mr. Yamanaka:Definitely. Machines such as saws for cutting wooden materials or sanders for polishing the surface were quite basic, but these are still being in use today without any problems. So, I guess they already had the technical capabilities to build durable and long-lasting machines back then. It's not just about the high technical skills, but we must also consider the fact that generations of workers maintained each and every equipment with great care. That's one of the reasons why we are still able to use these machines after 50 years.
JP2:Maruni Wood Industry had the high technical skills to industrialize back in those days. Did any company request you to make machines for them, using your manufacturing skills and know-hows?
Mr. Yamanaka:We never received any orders, but we were one of the few companies which have automated, back then. Therefore, we received consultations from companies in various industries, and the founder actually went to many of them to offer technical guidance. In a way, we were one of the first pioneering companies that succeeded in "industrialization," which most companies were unable to do.
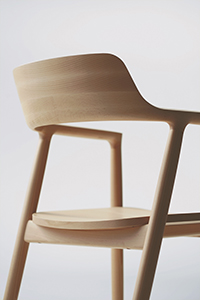
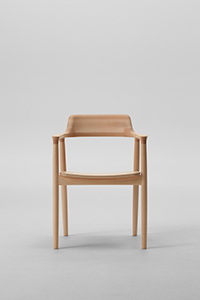
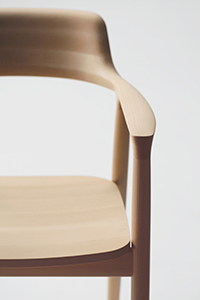
JP2:You guys were really committed to "the industrialization of craftsmanship" from back then.
Mr. Yamanaka:Definitely. The founder had the aspiration of raising the level of Japanese housing culture through mass production of furniture, during the period when they only had floors and tatami mats. However furniture back then was pricy, and not everyone was able to easily afford it. Industrialization or optimization of furniture manufacturing is, in short, mass production. By doing so, we can drop the price. Those things allow us to industrialize without losing our craftsmanship. The founder was the one who was serious about achieving it. If someone were to ask me who I'd like to meet, I would definitely want to meet the founder the most. I would like to ask him, about the things he was thinking back then and how he had so much passion towards furniture and craftsmanship.
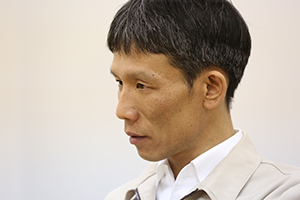
JP2:Since its establishment, Maruni Wood Industry has manufactured numerous furniture. Are there anything that has been passed on until this day?
Mr. Yamanaka:Definitely, our motto: "Industrialization of craftsmanship." We began mass producing furniture which previously could only be afforded by the upper class. However, the “essence” of the furniture cannot be expressed through mass production, so we had to industrialize our craftsmanship effectively. I believe, we have carefully maintained such balance until now. Up to this day, we have been working hard to survive as a manufacturer. This balance is what we carefully maintain and are always strongly aware of.
But, it's not the case that we constantly kept this in ours minds, working through the years. There was a period when our annual revenue peaked over 30 billion yen; the so-called "Bubble economy." And we were forced to feel the backlash when the bubble popped. As a result, the Chinese and Thai factories were constructed for cheap labor cost. Our structure shifted to making "manufactured products." The other furniture manufacturers did not take such strategy, so our sales recovered momentarily. But things like that can be easily imitated. For that reason, our sales began to slowdown. Since we have been working hard to survive as a manufacturer, we were convinced that cannot remain in this position for long. What we provide the customers aren't industrial products but furniture. We shouldn't automate just for the sake of reducing the cost. I reaffirmed myself that we need to work towards "the industrialization of craftsmanship." I would like to pass this spirit down, as it is, within our company.
JP2:Presently, you have parted with the factories in Thailand and China, and concentrated them in Japan. Tell us the number 1 reason for doing so.
Mr. Yamanaka:Before working here, I was a banker who was in charge of dealing with NPL (non-profit loans). For that reason, when I saw the financial reports and the economical situation of this company, I thought this company won't last that long. That's how severe the business condition was at that time. Back then, I was completely focused on how to improve the situation, and was anxious of making profit in some way. And originally, I wasn't really into design, wooden products, or furniture. When such type of person comes into a company, the first thing he does is lay off people. But now, as an employer, I really regret doing such horrible things to the people who worked here. When we were in such tough economical situation, I thought the factories in Thailand and China were our strengths. By training them adequately, we were able to manufacture quality products at a low cost. But gradually, I noticed that the atmosphere in the Japanese and the overseas factories were different. And then I realized that the difference came from the difference in the attitudes of the craftsmen, towards making furniture.
The Japanese craftsmen are people who honestly love working with furniture. As I worked with these people, I got drawn into (or maybe tricked me into liking) wooden products and furniture, which I was never interested in, and I started to really like them. At the Japanese factories, we have craftsmen who are serious about their craft and pour their soul when they make the furniture.
Unfortunately, I couldn't find many people who had the feeling towards furniture like them, in the factories overseas. The factories were basically built to make cheap furniture, so I wasn't able to give orders other than "make them cheap." Consequently, the products made in Thai and Chinese factories weren't like the "soulful" furniture from Japanese factories. I thought it was pointless to keep those factories, so we sold them and brought all the factories to Hiroshima.
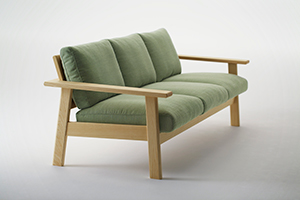
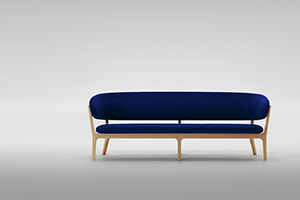
JP2:You said that you were only able to give orders to "make them cheap" and also they weren't able to make quality products. Was difference in language a factor causing the problems between Maruni Wood Industry and the overseas factories? Or was it the difference in the cultural backgrounds?
Mr. Yamanaka:I felt like it was the cultural difference. I'm not interested in actively promoting "made in Japan" overseas. It's because if we say our products are "made in Japan," we might just end up putting lacquers and using Nishijin fabrics on them. But instead, let's say that we have a nice chair. And a foreigner touches it and sits on it and suddenly looks up at our Asian faces and says, "Are you guys Japanese?" That's the moment I feel great! Like, "Wow, the Japanese can do fine jobs." I think this is the true sentiment of "made in Japan." Maybe, there's something "Japanese" contained within our furniture. That's what I feel, what I want to feel, and what many of our customers are actually feeling. I'm not directly involved with the manufacture, but I really respect our craftsmen. Such attitude towards Japanese craftsmanship, couldn't be easily communicated in our overseas factories. That's why I felt more of a difference in cultures and ideas than in our languages.
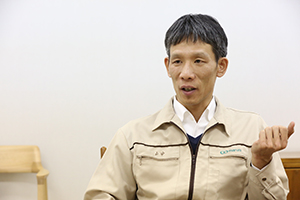
JP2:So, Maruni craftsmen work with pride and the spirit of craftsmanship.
Mr. Yamanaka:Definitely. I hope they work with that kind of attitude. When I joined the company, the policy was to make things that sell. So, what they did was, they built factories in Thailand and China. Various types of furniture were made, but I still clearly recall how I wondered, “who was actually going to buy these things?” As long as we make things in that way, the craftsmen wouldn't say "we are the ones who made this," and they won't have pride in their furniture. Using an example from nowadays, the craftsmen at the first station of the manufacturing process, aren't just cutting the wooden boards to certain sizes and shapes, but they cut them so that the wooden grains can be easily matched at the next station. Whichever station they are working in, they pay close attention to details while they work. "Such effort in their work results in the arms with symmetrical grains." My job is to communicate that message to them, with the help of the marketing and R&D divisions. I need to continue reminding them that furniture crafted with fine details receives global recognition. By doing so, I believe that our staff of over 100, all of them, will put their heart and soul into making furniture. And also, I hope they can look at their furniture and feel proud of what they have accomplished.
JP2:Are you planning to continue the business, basing the factories in Hiroshima?
Mr. Yamanaka:Absolutely. Sentiments of Japanese craftsmen such as "the industrialization of craftsmanship," or the Japanese resourcefulness, to be more specific, our way of scrutinizing details, are what we would like to continue to pass down, here, in Hiroshima, as long as the social circumstance permits us. There are many manufacturers like that in Japan, and it is quite difficult to express in words what Maruni Wood Industry's characteristics are, but, they are definitely maintained at the work site. What really makes me happy is when our competitors come to visit our factory and tell us, "Maruni's finish is amazing!" What I believe makes a good finish, rests on a thin line of whether you polish things or not. So it may me negligible for our competitors, but it's not at Maruni. That's why when I think of keeping these values, I wanted to keep the factories in Hiroshima, Japan, where it all began.
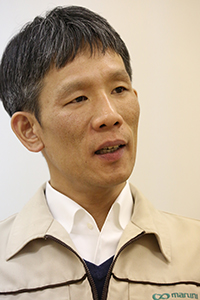
JP2:Lastly, share us your thoughts on Maruni Wood Industry.
Mr. Yamanaka:Our vision is "to continue manufacturing wooden furniture that will remain as the global standard, even after 100 years." Mr. Fukazawa was the one who mentioned about setting the global standard. When I heard these words I, quite frankly, felt them big and profound. Y chair is probably an example of wooden furniture that is the global standard, right now. But, those furniture were mostly made around 1950 and since then, there haven't been any chair that has set the global standard. Therefore, we want to make chairs that can be received as, "Hey! There's a chair that can become the new standard." Not just chairs, but we would like to make more furniture like that. We also have another vision. Since there aren't any globally established wooden furniture brands from Japan, we want to be the company that aspiring woodworkers from around the world want to visit. If that happens, we will need to open cafes, have factory tours for the general public, have workshops, construct accommodation facilities, and if we go even further, we will invite famous interior magazines from overseas into the mountains of Hiroshima. There, you will find many craftsmen working in ordinary work clothes. But, every craftsmen are really serious about their craft and they are absolutely awesome! If it changes into a place like that, the employees' pride and motivation will grow, and they will be able to produce things without compromise. There's a place like that in Denmark, where all of people involved in woodworking wish to visit. It will be really exciting if we can create such place here, where people from around the world would want to go. I believe, "Dream is pointless if it doesn't come true." And also, Maruni Wood Industry will be having its 100th anniversary in 13 years, so I'm thinking of working working hard to achieve the goal before that. However, I cannot accomplish it by myself, so I am really expecting that all of the staff of Maruni Wood Industry will work together to achieve this goal.
Maruni Wood Industry
Websitehttp://www.maruni.com/en/